El intervalo P-F para modos de falla de maquinarias
¿Sabías que podés medir el intervalo de tiempo que tenés para el próximo monitoreo de tu maquinaria? ¿Sabés cómo determinar ese intervalo? Para salir de dudas, acudimos a nuestros expertos, quienes elaboraron una serie de consejos a seguir. Te los contamos en este blog. En primer lugar, el intervalo P-F se usa para determinar el intervalo efectivo para tareas de monitoreo. A su vez, el monitoreo de condición se usa para detectar la degradación antes que un equipo falle funcionalmente. Para realizar tareas efectivas, es esencial poseer una buena comprensión del intervalo P-F.
En ese sentido, las tareas efectivas poseen un intervalo que es la mitad del período de tiempo entre el punto P donde el deterioro se considera detectable / medible y el punto F donde el componente falla.
En resumen, el intervalo de monitoreo es la mitad de P-F. Para modos de falla creíbles, con consecuencias graves, normalmente se aplica un tercio de P-F.
Condiciones
Para que las tareas de monitoreo de condición sean efectivas, deben satisfacerse algunos criterios, incluyendo:
-
El deterioro de la condición debe ser detectable y cuantificable (punto P): Es fundamental que cualquier signo de deterioro sea identificable a través de técnicas de monitoreo, ya sea mediante análisis de vibraciones, ultrasonidos, análisis de aceite o termografía.
-
Debe haber suficiente tiempo disponible para responder (o ciclos de trabajo) y evitar las consecuencias de la falla funcional: Esto asegura que las acciones correctivas puedan ser implementadas antes de que ocurra una falla catastrófica.
-
El período entre la falla potencial (P) y la falla funcional (F) debe ser razonablemente previsible y constante: La consistencia en el intervalo P-F permite planificar y programar el monitoreo y las intervenciones de manera efectiva.
Intervalo P-F
Ejemplos
-
Fuga de Refrigerante en un Motor: Una pequeña fuga de refrigerante puede tener un intervalo P-F que varía de varios días a varios meses. Un intervalo de monitoreo óptimo es aproximadamente un mes.
-
Degradación en un Recipiente: En un recipiente con un espesor de pared de 20 mm, un pitting de 2 mm se considera evidencia de deterioro. Si no se detecta, podría llevar hasta 20 años para resultar en una falla real. Aquí, el intervalo P-F es de 20 años, por lo que el intervalo de inspección óptimo es de 10 años.
-
Falla de una Bombilla Eléctrica: Las bombillas eléctricas fallan en cuestión de segundos, con un intervalo P-F de solo 1 segundo. Por tanto, el monitoreo de condición no es efectivo para este tipo de falla repentina, aplicable también a muchos componentes electrónicos y eléctricos.
-
Cojinetes con Problemas de Lubricación: Un cojinete sin lubricación puede dañarse en 20 a 30 minutos. Con pérdida parcial de lubricación, el daño podría ocurrir en horas o días. Para una falla creíble por pérdida total de lubricación, el intervalo P-F es de 20 minutos, y el intervalo de monitoreo óptimo es de 10 minutos.
-
Sellos de Bombas: Un sello de bomba afectado por cavitación puede tener un intervalo P-F de 20 a 30 minutos, con un intervalo de monitoreo óptimo de 10 minutos. Pequeñas fallas de sellos tienen un intervalo P-F de horas a días, con un monitoreo óptimo de 1 a 2 horas.
-
Compresores: Los cojinetes de compresores pueden fallar en minutos tras la pérdida de lubricación. El intervalo de monitoreo es muy corto y normalmente se lleva a cabo mediante sistemas de monitoreo continuo.
-
Taponamiento de Filtros o Enfriadores de Aceite: Estos componentes pueden tener un intervalo P-F de varias semanas o meses. El intervalo de monitoreo se determina basándose en datos históricos del intervalo P-F.
Intervalo P-F en profundidad
Es crucial entender que los modos de falla creíbles con serias consecuencias y un intervalo P-F corto normalmente poseen una función de protección para mitigar la probabilidad de una falla funcional. Por ejemplo, los sistemas de protección de turbinas contra exceso de velocidad.
La estrategia de monitoreo de condición debe incluir técnicas que sean adecuadas para el intervalo P-F específico de cada componente. Por ejemplo, el análisis de aceite usado es efectivo para intervalos P-F amplios, ya que permite detectar cambios en tendencias. Sin embargo, para intervalos P-F cortos, técnicas de monitoreo continuo, como el monitoreo de vibraciones, son más apropiadas.
.
Tal vez te pueda interesar nuestro ebook
CONVIÉRTASE EN UN DETECTIVE DE CONFIABILIDAD DE SUS EQUIPOS
técnicas de monitoreo de condición
Existen diversas técnicas avanzadas para monitorear la condición de la maquinaria:
- Análisis de Vibraciones: Ideal para detectar desequilibrios, desalineaciones y defectos en rodamientos.
- Termografía Infrarroja: Utilizada para identificar puntos calientes en equipos eléctricos y mecánicos, lo que puede indicar fricción excesiva o aislamiento defectuoso.
- Análisis de Aceite: Permite detectar contaminación y desgaste excesivo en componentes internos.
- Ultrasonido: Útil para detectar fugas y arcos eléctricos.
Cada una de estas técnicas tiene sus ventajas y limitaciones, y la selección adecuada dependerá del tipo de equipo y del modo de falla que se está monitoreando.
conclusiones
Conocer el intervalo P-F de los modos de falla de su maquinaria es esencial para determinar la efectividad de las técnicas de monitoreo de condición. El análisis de aceite usado, por ejemplo, es muy efectivo cuando el intervalo P-F es lo suficientemente amplio para detectar cambios en tendencias, de lo contrario, se deben utilizar otras técnicas de monitoreo.
Siempre es recomendable consultar a un ingeniero especializado en lubricación y mantenimiento industrial para elegir la mejor alternativa de monitoreo para su maquinaria. Estas recomendaciones deben basarse en fuentes de alta reputación y en un entendimiento profundo de los principios de ingeniería aplicados al mantenimiento predictivo y proactivo. En Castrol podemos ayudarte.
.
Prevenir siempre es mejor que curar.
Solicite una asesoría especializada.
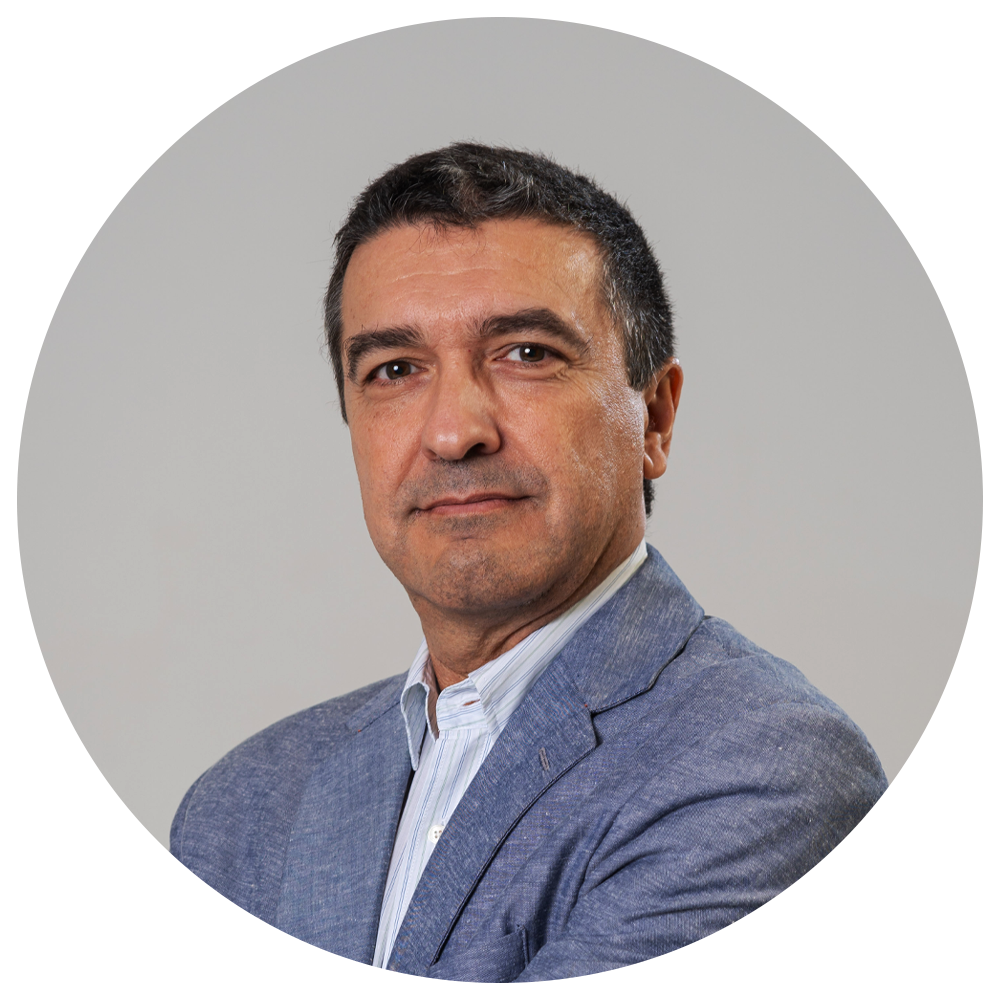
Ing. Marcelo Martins, gerente en Desarrollo Comercial