Mitos y verdades para mejorar la lubricación de sus equipos
La información es poder. Esta afirmación aplica para muchos ámbitos, incluso para la planificación del mantenimiento preventivo de los equipos. A continuación, vamos a derribar mitos infundados y creencias erróneas, para acercarnos a las mejores prácticas en lubricación de equipos.
Los programas de lubricación muchas veces se manejan sobre preconceptos y viejas premisas que arrastran inconsistencias acerca de cuáles son los mejores pasos a seguir. Si vamos a lo concreto, en materia de lubricación industrial debemos prestar atención a varios factores: desde el control de la contaminación de los lubricantes, el muestreo de los mismos para poder analizarlos y la programación de las tareas de lubricación, hasta la generación de procedimientos estándares y la capacitación del personal para crear un verdadero sistema de mejora continua.
En este último punto, nos referimos a una clásica premisa que dice que “los mejores programas de lubricación son los que involucran tanto a las personas que hacen el trabajo, como a toda la cadena de trabajo”. No importa en manos de quién esté la tarea de lubricación, es fundamental que todo equipo cuente con conocimientos básicos imprescindibles.
Fuente: Accelix |
Documentar procedimientos siempre puede aliviar golpes imprevistos, así que le recomendamos tener a mano estas buenas prácticas destacadas.
No todo es lo que parece
A continuación veamos algunos mitos que son tomados como verdades y no lo son tanto.
Mito N°1: Prevenir y mantener es costoso y lleva tiempo.
La experiencia nos dice que la principal razón detrás de esta falla es una percepción generalizada de que la ejecución de un plan de lubricación o mantenimiento adecuado consumiría mucho tiempo y sería muy costosa. ¡Error! Esta percepción es infundada y se mantiene a causa del desconocimiento.
Hoy la tecnología disponible podría dar lugar a una planificación estratégica que genere ahorros de tiempo y dinero sumamente significativos.
Mito N°2: Es mejor usar filtros reutilizables.
Otro de los erróneos métodos de ahorro más extendidos es la utilización de filtros metálicos lavables. En la práctica, este tipo de filtro mecánico definitivamente no posee eficiencia comprobada (no puede calcularse el parámetro del filtro), y por ende el sistema hidráulico no posee casi protección alguna.
Quienes fundamentan esta elección argumentan que los filtros de mayor eficiencia no solo se saturan rápidamente, sino que hacen caer la presión del sistema de manera intolerable. Pero, como sabemos, la innumerable cantidad de sistemas hidráulicos que utilizan filtros absolutos de 3 micrones con valores de eficiencia beta=1000 en todo el mundo son prueba de todo lo contrario.
Mito N°3: Cambiar filtros frecuentemente es una pérdida de tiempo.
Un tercer argumento clásico de quienes utilizan filtros lavables es que una empresa que trabaja en un ambiente muy polvoriento no puede darse el lujo de parar sus equipos para cambiar filtros. Sin embargo, sabemos que, con el tiempo, la consecuencia obvia de este razonamiento será la rotura de bombas, la aparición de fugas y la operación errática del sistema.
Con toda esta información sobre la mesa podemos decir que implementar un sistema adecuado de exclusión de la contaminación en estos equipos sin duda presenta algunos retos más que en una empresa que trabaja en ambientes menos polvorientos, pero claramente los beneficios serán aún mayores y medibles.
Quizás te interese seguir leyendo
PIRAMIDE DE CONFIABILIDAD: BUENOS DISEÑOS, OPERACIÓN Y REPARACIONES
4 buenas prácticas para la lubricación de los equipos
Ahora si vayamos, entonces, a las prácticas que sí marcan la diferencia:
- Lubricación adecuada: Cuando a un activo le falta grasa, rápidamente reconoceremos el problema, generalmente por una falla. Sin embargo, el exceso de grasa no es tan visible pero puede tener un efecto similar. Por eso es importante recordar que los lubricantes tienen volumen propio y es preciso suministrarlos en proporciones adecuadas: demasiado o muy poco podría causar que un activo requiera mantenimiento adicional y horas de inactividad.
- Lubricante correcto: El uso del lubricante incorrecto no solo puede provocar fallas en los activos, sino que también puede anular la garantía de la maquinaria. Conocer estas pautas es crucial para un buen funcionamiento y evitar presupuestos adicionales para la reparación de equipos.
- Sin mezclar jamás: No todos los lubricantes son iguales y mezclar tipos incorrectos puede llegar a ser tan dañino como no lubricar en absoluto. Mezclar lubricantes sintéticos y minerales incompatibles, por ejemplo, puede causar problemas desde fugas hasta fallas en los equipos industriales, corriendo el riesgo de expandir o contraer los sellos cercanos. Algo similar ocurre cuando se agrega un espesante incompatible a la grasa, porque la mezcla puede volverse inestable e inapropiada para su uso en la mayoría de las máquinas.
- Monitoreo preventivo. Evitar la contaminación de lubricantes es fundamental, y hay que saber que la misma puede provenir de partículas en el aire ambiente, suciedad del exterior de la instalación o de agentes dentro de la propia máquina. Es importante sumar protocolos de limpieza para garanticen que la contaminación tenga un impacto mínimo en el tiempo de actividad de los activos. Una herramienta de ultrasonido puede identificar discrepancias en la salida ultrasónica de un rodamiento, notificando al personal de mantenimiento con mucha anticipación sobre la falla del equipo.
Buenas prácticas en acción
Se han detallado los pilares que forman parte de una verdadera ingeniería líquida eficiente. A continuación, algunas consideraciones prácticas específicas que también podemos implementar:
- Utilizar un carro filtrante portátil para colocar el aceite nuevo.
- Colocar filtros de alta eficiencia en la cantidad y tamaño adecuados.
- Generar procedimientos y documentarlos por escrito
- Implementar un programa de análisis periódico.
En suma, contar con la información adecuada marca la diferencia. Por eso un programa de lubricación mejorado comienza con datos precisos y con un equipo de trabajo que tenga información disponible para poder tomar buenas decisiones, también con metodologías como puede ser la pirámide de confiabilidad. Así se podrán lograr procesos de revisión y previsión constantes que optimicen los resultados, generen ahorros de mantenimiento y, por sobre todo, que eviten la rotura de componentes, así como fugas y operaciones erráticas. Este es el camino para evitar costos asociados a las paradas imprevistas, que tantas complicaciones traen aparejadas.
¿Tienes dudas?
Recibe una asesoría de uno de nuestros especialistas.
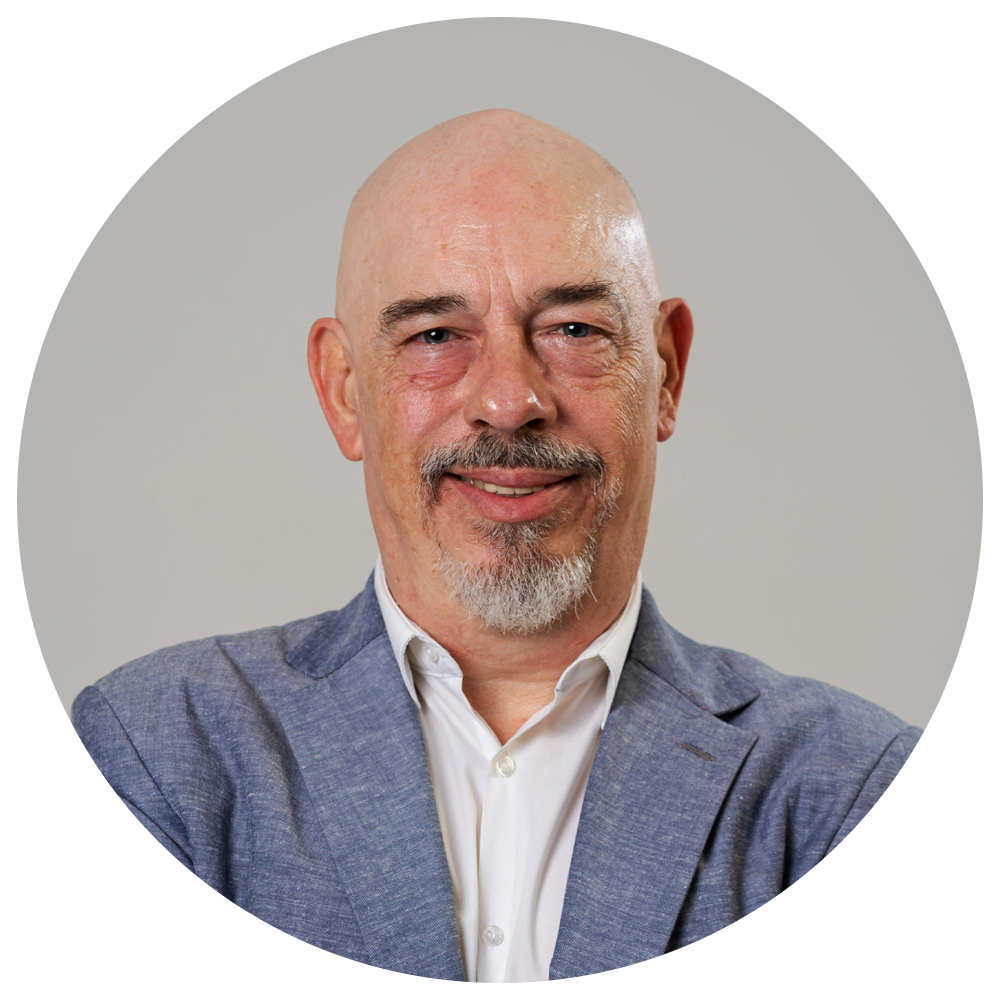
Ing. Fernando Bilotti, especialista en Desarrollo Comercial